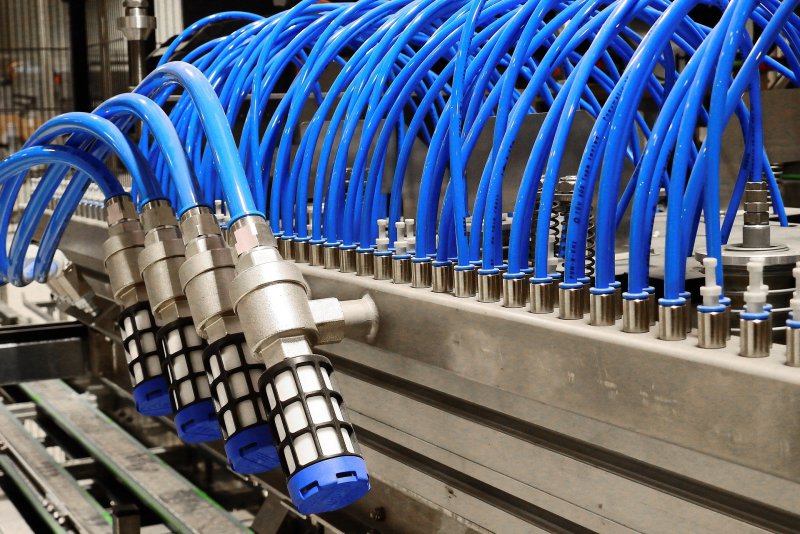
Wysokie zużycie, kosztowna konserwacja, wysokie koszty energii - istnieje wiele mitów na temat siłowników pneumatycznych, które sprawiają, że technologia ta wydaje się mniej korzystna niż inne alternatywne rozwiązania. W niektórych przypadkach wynika to z błędnych przekonań lub przestarzałych obliczeń. W innych przypadkach wynika to z faktu, że wady, które odgrywają rolę w określonych zastosowaniach i branżach, są przenoszone na konkretny przypadek. Dlatego zawsze warto przyjrzeć się bliżej: jakie dokładnie jest zastosowanie?
Ten blog bierze pod lupę cztery rozpowszechnione założenia i na podstawie aktualnego stanu wiedzy sprawdza, czy są one prawdziwe. Tyle możemy powiedzieć: we wszystkich przypadkach odpowiedź nie jest tym, czym wydaje się na pierwszy rzut oka.
Mit #1: Pneumatyka oznacza więcej komponentów. W rezultacie, technologia ta technologia ma zwiększone zużycie i dlatego wymaga droższej konserwacji.
System pneumatyczny wymaga całego szeregu komponentów do wytwarzania sprężonego powietrza: są to sprężarka, osuszacz i zbiornik powietrza. Ponadto do transportu i przełączania sprężonego powietrza do odpowiednich elementów wykonawczych potrzebne są rury, przewody i zawory. Na pierwszy rzut oka wydaje się, że liczba akcesoriów, a tym samym koszty konserwacji i ryzyko zużycia są zwielokrotnione.
Sprężarka wymaga konserwacji tylko raz w roku
Wytwarzanie sprężonego powietrza jest jednak wymagane tylko raz. Jedna sprężarka może bez problemu zasilać jednocześnie kilkaset siłowników. Na przykład w przeciętnej komunalnej stacji uzdatniania wody znajduje się zazwyczaj od 50 do 200 siłowników. Podczas gdy w dużych zakładach przemysłowych do zasilania siłowników pneumatycznych stosuje się sprężarki śrubowe, które są przystosowane do pracy ciągłej, w gospodarce wodnej stosuje się sprężarki tłokowe, które są urządzeniami poręcznymi i można je transportować na przykład na palecie. Wynika to z faktu, że zużycie sprężonego powietrza w stacjach uzdatniania wody jest stosunkowo niewielkie. Wiele zaworów procesowych musi być przełączanych tylko raz dziennie. Oznacza to, że sprężarka również nie wymaga dużych nakładów na konserwację - wystarczy ją serwisować tylko raz w roku.
Siłowniki pneumatyczne są również odporne na wibracje i mają dożywotnie smarowanie. Wszystko to oznacza, że siłownik pneumatyczny jest całkowicie bezobsługowy. Kolejną zaletą jest to, że siłownik pneumatyczny ma możliwość pracy ciągłej, a więc nie potrzebuje faz chłodzenia jako okresów odpoczynku, jak siłownik elektryczny. Innymi słowy - siłownik pneumatyczny jest pod każdym względem trwalszy.
Uwaga |
W siłownikach pneumatycznych występują pewne straty energii, ale nie większe niż w siłownikach alternatywnych. Pozostałe obliczenia opierają się na przestarzałych metodach. W dzisiejszych czasach nieszczelności są w większości przypadków minimalne, a ich lokalizacja i naprawa jest łatwa i tania. |
Mit #2: Sprawność układów pneumatycznych jest bardzo niska. Większość energii jest tracona w postaci ciepła. Do tego dochodzi energia tracona z powodu nieszczelności.
Wyniki badań przeprowadzonych w latach dziewięćdziesiątych utwierdziły wielu w przekonaniu, że siłowniki pneumatyczne mają sprawność zaledwie 7% - co oznaczałoby, że 93% energii generowanej przez sprężarkę jest tracone. Jednak już w momencie publikacji tego opracowania (Ilmberger/Seyfried, BWK, 1994) brakowało potwierdzonych informacji. Z dzisiejszego punktu widzenia to 24-letnie opracowanie można jednak zdecydowanie uznać za nieistotne, ponieważ zostało przeprowadzone na podstawie przestarzałego systemu.
Faktem jest, że systemy sprężonego powietrza, podobnie jak inne systemy, charakteryzują się pewnymi stratami energii, począwszy od sprężarki, poprzez osuszacz chłodniczy, aż do przyłącza odbiorcy. W najnowszym opracowaniu dotyczącym nowoczesnego systemu (EnEffAH - Energieeffizienz in der Produktion im Bereich Antriebs- und Handhabungstechnik, 2012) stwierdzono, że całkowity pobór energii daje 42,1 procent efektywności użytkowej, jak pokazano w tabeli 1.
Nieszczelności nie są czymś, z czym musimy się godzić
W obiegu znajdują się również różne liczby dotyczące nieszczelności, które z dzisiejszej perspektywy nie są już możliwe do utrzymania. Obecnie bardziej niż kiedykolwiek nacisk kładzie się na monitorowanie zużycia sprężonego powietrza i wykrywanie nieszczelności - ich znaczenie rośnie. Duże przedsiębiorstwa mają obecnie własne systemy zarządzania energią i dokonują regularnych pomiarów.
Mit #3: Pneumatyka może być tańsza w zakupie, ale jest droższa w przeliczeniu na cały okres eksploatacji.
Przy porównywaniu różnych siłowników pneumatycznych, elektrycznych i hydraulicznych nadal pokutuje przekonanie, że choć na pierwszy rzut oka siłowniki pneumatyczne mogą być tańsze, to w przeliczeniu na cały okres eksploatacji ich koszty są znacznie wyższe. W rzeczywistości zależy to jednak w dużym stopniu od zastosowania.
Na przykład w branży wodno-kanalizacyjnej, która wykorzystuje siłowniki z najwyższą wydajnością w trybie pracy ciągłej, koszty eksploatacyjne układów pneumatycznych i elektrycznych są zupełnie inne niż w przypadku oczyszczalni ścieków, która średnio otwiera lub zamyka siłowniki i zawory procesowe. W przypadku tej ostatniej koszty eksploatacyjne są pomijalnie małe w porównaniu z kosztami inwestycyjnymi.
Jak pokazano w tabeli 2, rozwiązanie pneumatyczne jest bez wątpienia tańsze, jeśli chodzi o koszty inwestycyjne: około 159 000 EUR w porównaniu z około 222 000 EUR w przypadku siłownika elektrycznego. Dla kosztów energii podczas eksploatacji przyjęto, że filtr jest płukany raz w tygodniu (wymaga to jednokrotnego otwarcia wszystkich zaworów procesowych i ponownego ich zamknięcia). Wynikiem tego jest stosunkowo krótki czas pracy, który jest jednak reprezentatywny dla branży i jej zastosowań.
Całkowity koszt posiadania wynosi ok. 200.000 EUR w przypadku systemu pneumatycznego i 295.000 EUR w przypadku systemu z elektrycznym siłownikiem zaworu. Do tego dochodzą jeszcze koszty przeglądów i konserwacji oraz ostatecznego demontażu w fazie utylizacji. Koszty inwestycyjne są więc w tym przykładzie znacznie wyższe, a koszty uzupełniające wynoszą zaledwie 20 do 30 procent. Całkowity koszt posiadania rozwiązania pneumatycznego jest więc o prawie jedną trzecią niższy.
Mit #4: Elementy pneumatyczne, takie jak przewody rurowe, są skomplikowane w instalacji i dodatkowo podatne na wycieki.
Połączenie pomiędzy zaworem elektromagnetycznym a siłownikiem jest obecnie realizowane za pomocą połączenia rurowego i złączki wciskanej. Dla każdego zastosowania dostępna jest odpowiednia kombinacja. Wszystkie te kombinacje mają jedną wspólną cechę: są łatwe w układaniu i niezawodne w montażu. Rurka jest wprowadzana do złączki jednym ruchem i przytrzymywana pewnie przez nierdzewny pazur mocujący, który nie uszkadza powierzchni. Wibracje i skoki ciśnienia są w ten sposób bezpiecznie absorbowane. Pierścień uszczelniający gwarantuje doskonałe uszczelnienie pomiędzy rurą a złączką. Kompletny montaż może być przeprowadzony bez konieczności angażowania specjalisty.
Obecne komponenty są wytrzymałe i łatwe w obsłudze
Wciąż utrzymująca się obawa, że połączenie rurki i złączki push-in jest podatne na przeciekanie, jest dziś bezpodstawna, zwłaszcza w obliczu różnorodności produktów i wysokiej jakości komponentów. Kombinacja ta nadaje się nawet do stosowania w próżni.
Zaleta, która często jest pomijana: niezawodność
Idealny system to taki, który zawsze działa - bez problemów, bez przerw i bez awarii. Jednak każdy operator zakładu wie, że jest to ostatecznie utopia. Większość systemów łączy w sobie zbyt wiele złożonych czynników, aby mogły one działać bezawaryjnie przez cały okres eksploatacji. Czy to "czynnik ludzki", czyli błąd pracownika, czy też zupełnie zewnętrzne, również nieprzewidywalne wpływy, takie jak awaria zasilania elektrycznego czy pogoda.
Siłowniki pneumatyczne wykazują w tym kontekście mocną stronę, o której niektórzy planiści nawet nie myślą: są one niezwykle odporne na wiele z tych nieobliczalnych czynników - i można je stosunkowo łatwo naprawić lub przełączyć za pomocą awaryjnych materiałów eksploatacyjnych.
Elastyczna reakcja na nieprzewidywalne sytuacje
Na przykład w przypadku awarii zasilania: sprężone powietrze jest dostępne również w przypadku awarii zasilania. Oprócz sprężarki zawsze dostępny jest także zbiornik sprężonego powietrza. W ten sposób można łatwo pokonywać przerwy w dostawie prądu - w zależności od wymaganego zużycia sprężone powietrze może być wykorzystywane jeszcze przez pewien czas, nawet jeśli nie ma zasilania.
Napędy pneumatyczne umożliwiają elastyczne reagowanie na wiele typowych, nieprzewidywalnych sytuacji, np. jeśli zasuwa wymaga chwilowo większej mocy ze względu na osady, które z czasem zebrały się na zasuwie, można to bardzo łatwo osiągnąć poprzez zwiększenie ciśnienia.
Jeżeli w dowolnym miejscu siłownika rzeczywiście wystąpi usterka, można przeprowadzić wstępną kontrolę bez konieczności angażowania specjalistów. W przeciwieństwie do siłowników elektrycznych, w przypadku których w razie awarii konieczna jest konsultacja z elektrykiem, nieszczelności i wymiana uszczelek mogą zostać wykryte bez konieczności posiadania specjalistycznej wiedzy. Pomijając fakt, że siłowniki pneumatyczne są znacznie bardziej wytrzymałe ze względu na stosunkowo prostą konstrukcję, są one odporne na przeciążenia, nie mogą się przegrzewać i nie wymagają ochrony silnika ani faz chłodzenia.