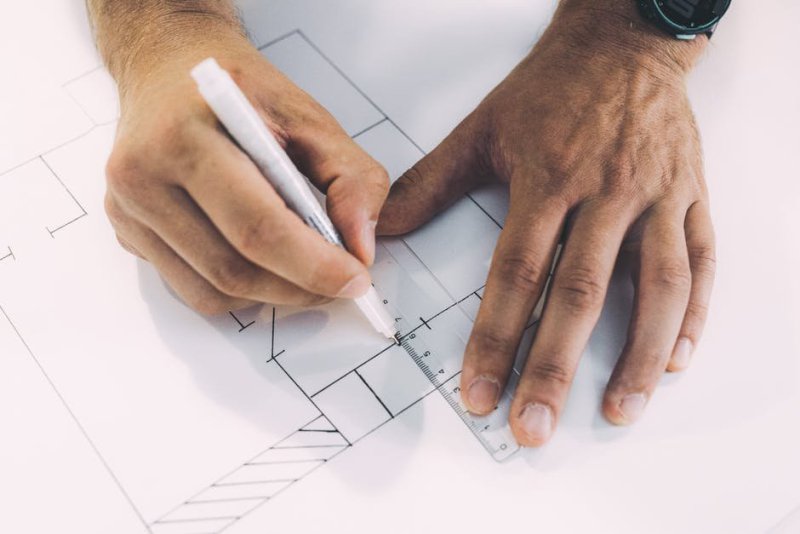
Dokładność obróbki odnosi się do stopnia, w jakim rzeczywiste parametry geometryczne (wielkość, kształt i położenie) części po obróbce są zgodne z idealnymi parametrami geometrycznymi określonymi na rysunkach. Im wyższy jest stopień tej zgodności, tym wyższa jest dokładność obróbki.
W obróbce skrawaniem, ze względu na wpływ różnych czynników, w rzeczywistości nie jest możliwe, aby każdy parametr geometryczny części był całkowicie zgodny z idealnym parametrem geometrycznym i zawsze będą występować pewne odchylenia. Odchylenia te to właśnie błędy obróbki.
Dzisiaj przedstawimy trzy następujące aspekty:
- Metody uzyskiwania dokładności wymiarowej części
- Metody uzyskiwania dokładności kształtu
- Jak uzyskać dokładność położenia?
Metody uzyskiwania dokładności wymiarowej części
(1) Metoda próbnego skrawania
Oznacza to, że najpierw należy spróbować wyciąć niewielki fragment obrabianej powierzchni, zmierzyć wielkość uzyskaną przez cięcie próbne, wyregulować położenie krawędzi skrawającej narzędzia względem przedmiotu obrabianego zgodnie z wymaganiami obróbki, następnie spróbować wykonać cięcie, a następnie dokonać pomiaru, po dwóch lub trzech próbnych cięciach i pomiarach, gdy maszyna jest obrabiana Po osiągnięciu wymaganej wielkości, wycina się całą obrabianą powierzchnię.
Metoda próbnego skrawania jest powtarzana aż do uzyskania wymaganej dokładności wymiarowej poprzez "próbne skrawanie-pomiar-regulację-powtórne skrawanie". Przykładem może być próbna obróbka wytaczania w systemie otworów skrzynkowych.
Precyzja osiągana metodą próbnego cięcia może być bardzo wysoka, nie wymaga skomplikowanych urządzeń, ale metoda ta jest czasochłonna (wymaga wielokrotnych regulacji, próbnego cięcia, pomiarów, obliczeń), mało wydajna i zależy od poziomu technicznego pracowników oraz dokładności przyrządów pomiarowych, a jej jakość jest niestabilna, dlatego stosuje się ją tylko w produkcji jednostkowej, małoseryjnej.
Jako rodzaj metody próbnego cięcia - dopasowywania, opiera się na przetworzonym detalu, przetwarzając inny pasujący detal lub metodę łączenia dwóch (lub więcej) detali do przetwarzania. Wymagania dotyczące ostatecznego rozmiaru przedmiotu obrabianego w procesie dopasowania są oparte na wymaganiach dotyczących dopasowania obrabianych części.
(2) Metoda regulacji
Dokładne pozycje względne obrabiarek, zamocowań, narzędzi i przedmiotów obrabianych są z wyprzedzeniem regulowane za pomocą próbek lub części standardowych, aby zapewnić dokładność wymiarową przedmiotu obrabianego. Ponieważ wymiar jest regulowany z wyprzedzeniem, podczas obróbki nie ma potrzeby próbowania cięcia, wymiar jest uzyskiwany automatycznie i pozostaje niezmienny podczas przetwarzania partii części - jest to metoda regulacji. Na przykład podczas stosowania zamocowania frezarki położenie narzędzia jest określane przez blok ustawiania narzędzia. Istotą metody regulacji jest zastosowanie urządzenia o stałym zakresie lub urządzenia do ustawiania narzędzi na obrabiarce albo wstępnie ustawionego uchwytu narzędziowego, aby narzędzie osiągnęło określoną dokładność pozycjonowania względem obrabiarki lub zamocowania, a następnie obróbka partii przedmiotów.
Podawanie narzędzia na obrabiarkę zgodnie z tarczą, a następnie skrawanie, jest również rodzajem metody regulacji. W tej metodzie należy najpierw określić skalę na tarczy zgodnie z metodą próbnego cięcia. W produkcji masowej do regulacji często wykorzystuje się urządzenia do ustawiania narzędzi, takie jak ograniczniki o stałym zakresie, próbki i szablony.
Metoda ustawiania charakteryzuje się lepszą dokładnością i stabilnością obróbki niż metoda próbnego skrawania, a także wyższą wydajnością. Nie wymaga ona wysokiej klasy operatorów obrabiarek, ale ma wysokie wymagania wobec pracowników zajmujących się ustawianiem obrabiarek. Jest ona często stosowana w produkcji seryjnej i masowej.
(3) Metoda doboru wielkości
Metoda polegająca na wykorzystaniu odpowiedniego rozmiaru narzędzia w celu zapewnienia rozmiaru obrabianego przedmiotu nazywana jest metodą wymiarowania. Obróbka odbywa się przy użyciu narzędzia o standardowym rozmiarze, a rozmiar obrabianej powierzchni jest określany przez rozmiar narzędzia. Oznacza to, że narzędzie o określonej dokładności wymiarowej (np. rozwiertak, wiertło rozwiercające, wiertło itp.) jest używane do zapewnienia dokładności obrabianej części (np. otworu) przedmiotu obrabianego.
Metoda wymiarowania jest łatwa w obsłudze, ma wysoką wydajność i stosunkowo stabilną dokładność obróbki. Nie ma ona prawie nic wspólnego z poziomem technicznym pracowników i charakteryzuje się wysoką wydajnością. Jest ona szeroko stosowana w różnych rodzajach produkcji. Takich jak wiercenie, rozwiercanie itp.
(4) Aktywna metoda pomiaru
W procesie obróbki mierzy się wielkość obróbki podczas obróbki i porównuje zmierzone wyniki z wielkością wymaganą w projekcie lub powoduje, że obrabiarka kontynuuje pracę lub zatrzymuje się - jest to metoda pomiaru aktywnego.
Obecnie wartości w pomiarze aktywnym mogą być wyświetlane cyfrowo. Metoda pomiaru aktywnego dodaje urządzenie pomiarowe do systemu procesowego (tj. jedności obrabiarki, narzędzia, zamocowania i przedmiotu obrabianego), który staje się jego piątym czynnikiem.
Aktywna metoda pomiarowa charakteryzuje się stabilną jakością i wysoką wydajnością, co stanowi kierunek rozwoju.
(5) Metoda sterowania automatycznego
Metoda ta składa się z urządzenia pomiarowego, urządzenia podającego i systemu sterowania. Jest to automatyczny system przetwarzania składający się z urządzenia pomiarowego, urządzenia podającego i systemu sterowania, a proces przetwarzania jest realizowany automatycznie przez system.
Szereg zadań, takich jak pomiar wymiarów, regulacja kompensacji narzędzia, skrawanie i parkowanie obrabiarki, jest wykonywanych automatycznie w celu automatycznego osiągnięcia wymaganej dokładności wymiarowej. Na przykład podczas obróbki na obrabiarce CNC części sterują sekwencją obróbki i dokładnością obróbki za pomocą różnych instrukcji programu.
Metody uzyskiwania dokładności kształtu
1) Metoda trajektorii
Ta metoda obróbki wykorzystuje trajektorię ruchu końcówki narzędzia do formowania kształtu obrabianej powierzchni. Zwykłe toczenie, frezowanie, struganie i szlifowanie należą do metody trajektorii końcówki narzędzia. Dokładność kształtu uzyskiwana w tej metodzie zależy głównie od dokładności ruchu formującego.
2) Metoda kształtowania
Kształt obrabianej powierzchni uzyskuje się, wykorzystując geometrię narzędzia formującego do zastąpienia niektórych ruchów formujących obrabiarki. Takich jak toczenie, frezowanie, szlifowanie itp. Dokładność kształtu uzyskiwana w metodzie formowania zależy głównie od kształtu krawędzi skrawającej.
3) Metoda rozprężania
Kształt obrabianej powierzchni uzyskuje się, wykorzystując powierzchnię obwiedniową utworzoną przez ruchy generujące narzędzia i przedmiotu obrabianego, np. frezowanie kół zębatych, kształtowanie kół zębatych, szlifowanie kół zębatych, radełkowanie itp. Dokładność kształtu uzyskana tą metodą zależy głównie od dokładności kształtu ostrza i dokładności ruchu wytwarzającego.
Jak uzyskać dokładność położenia
W obróbce skrawaniem dokładność położenia obrabianej powierzchni względem innych powierzchni zależy głównie od zamocowania przedmiotu obrabianego.
1) Bezpośrednie szukanie formalnego zacisku
Ta metoda jest metodą mocowania, w której położenie przedmiotu obrabianego jest bezpośrednio lokalizowane na obrabiarce za pomocą czujnika zegarowego, tarczy traserskiej lub kontroli wzrokowej.
2) Zaznaczenie linii w celu znalezienia właściwego zacisku
Ta metoda polega na narysowaniu na półwyrobach linii środkowej, linii symetrii i linii obróbki każdej obrabianej powierzchni zgodnie z rysunkiem części, a następnie zainstalowaniu przedmiotu na obrabiarce i ustawieniu pozycji zamocowania przedmiotu na obrabiarce zgodnie z narysowaną linią.
Ta metoda mocowania charakteryzuje się niską wydajnością, niską precyzją i wysokim poziomem technicznym pracowników. Stosuje się ją zazwyczaj do obróbki złożonych i ciężkich części w produkcji jednostkowej małych serii lub gdy tolerancja wymiarów półwyrobu jest duża i nie można go bezpośrednio zamocować za pomocą uchwytu.
3) Zaciskanie za pomocą przyrządu
Oprzyrządowanie jest specjalnie zaprojektowane zgodnie z wymaganiami procesu, który ma być przetwarzany. Elementy pozycjonujące w uchwycie mogą szybko zająć prawidłowe położenie przedmiotu względem obrabiarki i narzędzia, a dokładność zamocowania i pozycjonowania przedmiotu można zapewnić bez konieczności osiowania. Dokładność pozycjonowania jest wysoka, ale wymaga zaprojektowania i wykonania specjalnych uchwytów, które są powszechnie stosowane w produkcji seryjnej i masowej.