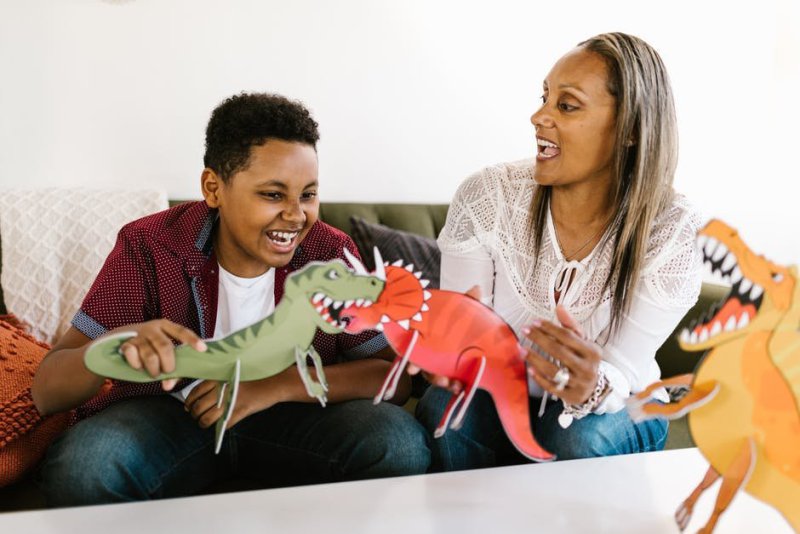
Aby spełnić wymagania dotyczące zamienności części w produkcji mechanicznej, wymiary produkowanych części powinny mieścić się w wymaganym zakresie tolerancji. Wymaga to ujednolicenia norm dotyczących formy, rozmiaru, dokładności i parametrów części. Podobne wyroby muszą być także racjonalnie sklasyfikowane pod względem wielkości, aby zmniejszyć liczbę serii wyrobów. Jest to standaryzacja wyrobów. Dlatego powstała koncepcja określania tolerancji inżynierskich i pasowań.
W inżynierii mechanicznej tolerancja określa dopuszczalne odchylenie od określonego wymiaru. Stosowanie tolerancji pomaga zapewnić, że wyrób końcowy jest łatwy w użyciu, zwłaszcza jeśli jest częścią większego zespołu.
Nieustalenie tolerancji w krytycznych obszarach może spowodować, że części nie będą mogły być używane zgodnie z założeniami projektowymi, ponieważ każda metoda wytwarzania charakteryzuje się pewnym stopniem niedokładności.
Jednak określenie odpowiednich tolerancji może sprawić, że firma produkcyjna będzie wiedziała, aby zwrócić większą uwagę na konkretne problemy podczas procesu produkcyjnego. Istnieje pewna zależność między częściami roboczymi: swobodny obrót, swobodny ruch wzdłużny, działanie mocujące, stałe położenie ustalone. Dokładność to dokładność wymagana do zapewnienia, aby część działała zgodnie z oczekiwaniami. Tolerancja to dopuszczalne odchylenie dowolnego rozmiaru w celu uzyskania prawidłowego działania.
Co to jest tolerancja konstrukcyjna?
Tolerancje inżynierskie to dopuszczalne odchyłki w pomiarach uzyskane z pomiarów podstawowych.
Załóżmy, że przetwarzany jest pręt metalowy o długości 100 mm. Mimo że wszystkie pręty stalowe mają być obrabiane do tego samego kształtu, to ze względu na rozmiar i kierunek prętów stalowych nie wszystkie można wyprodukować z dokładnością do 100,00 mm. Chociaż zakłady projektowe i produkcyjne ciężko pracują nad zmniejszeniem takich odchyleń, nadal nie można ich zniwelować do zera.
Ta odchyłka wielkości i kształtu w zasadzie waha się w górę i w dół wokół wartości docelowej. Dlatego górna i dolna wartość graniczna górnej wartości granicznej w stosunku do wielkości docelowej są określane na podstawie zastosowania pręta metalowego. Różnica (dopuszczalny zakres) pomiędzy tymi dwiema wartościami nazywana jest "tolerancją".
Tolerancje mogą być stosowane do wielu różnych jednostek. Na przykład, warunki pracy mogą mieć tolerancje dla temperatury (°C), wilgotności (g/m3) itp. W inżynierii mechanicznej tolerancje, o których głównie mówimy, odnoszą się do wymiarów liniowych, kątowych i innych wymiarów fizycznych. Niezależnie od jednostki, tolerancja wskazuje dopuszczalny zakres pomiaru od punktu bazowego (wartości nominalnej).
Rodzaje tolerancji inżynierskich
Tolerancje inżynierskie obejmują tolerancje wymiarów, tolerancje kształtu i tolerancje położenia.
Tolerancja wymiarowa
Tolerancja wymiarowa to dopuszczalna wielkość zmiany wielkości. Jest to podstawa tolerancji inżynierskich. Maksymalna dopuszczalna wartość nazywana jest wymiarem maksymalnym. Wartość minimalna jest nazywana wymiarem minimalnym.
Tolerancja jest wartością bezwzględną różnicy algebraicznej między maksymalnym górnym wymiarem granicznym a minimalnym górnym wymiarem granicznym oraz wartością bezwzględną różnicy algebraicznej między odchyleniem górnym a odchyleniem dolnym.
Odchylenie dolne
Dodanie dolnego odchylenia informuje producenta o tym, o ile może być mniejsza dana wartość pomiaru. Jest to oznaczane symbolem "-".
Odchylenie górne
Odchylenie górne jest przeciwieństwem odchylenia dolnego. Dodaje się ją, aby pokazać, o ile większa może być mierzona wartość od wartości nominalnej.
Bdchylenie boczne
Trzeci sposób podawania zakresu tolerancji polega na zastosowaniu odchylenia dwustronnego.
W przypadku tego samego rozmiaru podstawowego, im mniejsza tolerancja wymiarowa, tym większa dokładność wymiarowa. Określona tolerancja wskazuje na wymóg dokładności wykonania i odzwierciedla trudność obróbki.
Tolerancja kształtu
(1) Prostoliniowość
Prostoliniowość to warunek zachowania idealnej linii prostej przez rzeczywisty kształt elementów liniowych na części. Zwana także prostoliniowością. Tolerancja prostoliniowości to maksymalne dopuszczalne odchylenie rzeczywistej linii prostej od idealnej linii prostej. .
(2) Płaskość
Płaskość to odwzorowanie rzeczywistego kształtu elementów płaskich części w celu zachowania idealnej płaszczyzny. Jest to powszechnie określane jako płaskość. Tolerancja płaskości to maksymalna wielkość zmiany dopuszczalna przez rzeczywistą powierzchnię względem płaszczyzny.
(3) Okrągłość
Okrągłość to warunek, aby rzeczywisty kształt elementu części był równomiernie oddalony od jego środka. Okrągłość jest zwykle nazywana zaokrągleniem. Tolerancja okrągłości to maksymalna dopuszczalna odchyłka między okręgiem rzeczywistym a okręgiem idealnym w tym samym przekroju.
(4) Cylindryczność
Walcowość odnosi się do punktów na konturze cylindrycznej powierzchni części, przy zachowaniu równej odległości od jej osi. Tolerancja walcowości to maksymalne dopuszczalne odchylenie rzeczywistej powierzchni walca od idealnej powierzchni walca.
(5) Profil linii
Kontur linii to krzywa, która przedstawia dowolny kształt na danej płaszczyźnie części i zachowuje jej idealny kształt. Tolerancja konturu linii to dopuszczalna zmienność rzeczywistego konturu krzywej nieokrągłej.
6) Profil powierzchni
Profil powierzchni to powierzchnia dowolnego kształtu na części, która zachowuje swój idealny kształt. Kontur tolerancji powierzchni to dopuszczalne odchylenie między rzeczywistym konturem powierzchni nieokrągłej a konturem idealnym.
Tolerancja położenia
Tolerancja położenia odnosi się do całkowitej wielkości zmiany dopuszczalnej dla położenia określonego elementu względem układu odniesienia. Jest to kolejny ważny parametr tolerancji inżynierskiej.
(1) Tolerancja orientacji
Tolerancja orientacji odnosi się do całkowitej wielkości zmiany kierunku dozwolonej przez odniesienie związane z danym elementem. Tolerancja ta odzwierciedla równoległość, prostopadłość i kąt.
(2) Tolerancja położenia
Tolerancja położenia to pełny zakres zmienności położenia, który umożliwia powiązanie rzeczywistego elementu z odniesieniem. Tolerancje te obejmują współosiowość, symetrię i położenie.
(3) Tolerancja bicia
Tolerancja bicia to pozycja tolerancji określana zgodnie z określoną metodą testowania. Tolerancję bicia można podzielić na bicie po okręgu i bicie całkowite.
Pasowanie
Istnieje wiele różnych opcji pasowań wałków i otworów, a uzyskanie prawidłowego pasowania zawsze wymaga zachowania tolerancji. W montażu mechanicznym relacja pomiędzy otworem o tym samym podstawowym rozmiarze a strefą tolerancji wałka jest nazywana pasowaniem. Ponieważ rzeczywiste wymiary otworu i wałka są różne, po montażu wystąpi luz lub interferencja. W przypadku pasowania między otworem a wałkiem, gdy algebraiczna różnica wymiarów otworu minus wymiary wałka jest dodatnia, jest to luz, a gdy jest ujemna, jest to margines.
Istnieją trzy rodzaje pasowań inżynierskich otworu w wale.
Pasowanie luzu
Pasowanie to wymaga, aby średnica wałka była mniejsza niż średnica otworu. Oznacza to, że między nimi zawsze będzie występować szczelina.
Jeśli rozwiązanie inżynierskie wymaga, aby oba elementy mogły się przesuwać lub obracać niezależnie od siebie, należy zastosować ten sposób pasowania.
Dlatego w tym przypadku zarówno wałek, jak i otwór mają tolerancje, które mogą zapewnić ich nienakładanie się.
Pasowanie przejściowe
Ta opcja oznacza, że maksymalny rozmiar wałka jest większy niż minimalny rozmiar otworu. Jednocześnie minimalny rozmiar wałka jest mniejszy niż maksymalny rozmiar otworu.
Nie jest to więc pasowanie luzem ani pasowanie interferencyjne. Zgodnie z końcowymi wynikami pomiarów tolerancja pozwala na wystąpienie dwóch sytuacji, nie dopuszczając do sytuacji ekstremalnych.
Pasowanie interferencyjne
W tym przypadku średnica wałka jest zawsze większa niż średnica otworu. Nawet wtedy, gdy średnica wałka jest najmniejsza, a otworu największa.
Pasowanie interferencyjne zapewnia, że między tymi dwoma częściami nie ma żadnego ruchu. W procesie montażu fizycznego konieczne jest przyłożenie sił. Ogrzewanie otworów, zamrażanie wałków i stosowanie smaru ułatwiają ten proces.