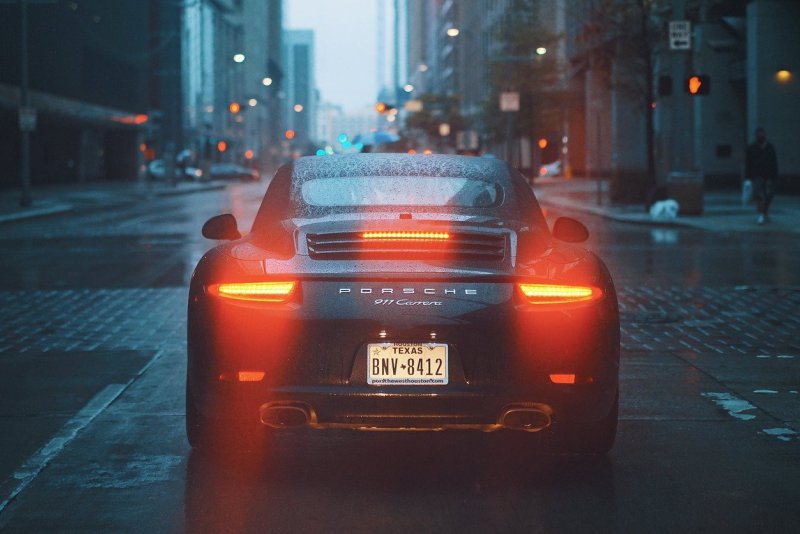
Jakość części powlekanych galwanicznie ma bezpośredni wpływ na ogólną jakość wyposażenia. Czynniki wpływające na jakość galwanizacji obejmują czynniki wewnętrzne i zewnętrzne. Dlatego konieczne jest nie tylko kompleksowe zrozumienie czynników wewnętrznych, które wpływają na jakość galwanizacji, ale także nie należy ignorować czynników zewnętrznych, które wpływają na jakość galwanizacji. Ścisła kontrola każdego ogniwa może zapewnić jakość galwanizacji.
Czynniki wpływające na jakość galwanizacji obejmują dwa aspekty: czynniki wewnętrzne i czynniki zewnętrzne:
1. Czynniki wewnętrzne
Ścisłe zarządzanie jakością w galwanizerni jest potężną gwarancją jakości elementów galwanizowanych. Aby zasadniczo poprawić jakość galwanizacji i uzyskać wysokiej jakości powłoki, należy dokładnie zrozumieć wszystkie wewnętrzne powiązania, które wpływają na jakość galwanizacji.
(1) Czynniki obróbki wstępnej
Siła wiązania, właściwości antykorozyjne i jakość wyglądu pomiędzy warstwą galwaniczną a podłożem są bezpośrednio związane z jakością obróbki powierzchni przed pokryciem galwanicznym. Olej, rdza, zgorzelina tlenkowa i inne zanieczyszczenia przytwierdzone do powierzchni części stanowią przeszkody pośrednie, które uniemożliwiają pełny kontakt roztworu galwanicznego z metalowym podłożem. Na takiej powierzchni nie jest możliwe utworzenie kwalifikowanej warstwy galwanicznej. Jeżeli do części galwanizowanych przylegają bardzo cienkie warstwy oleju i tlenków, to mimo że powłoka ma normalny wygląd i drobną krystaliczność, siła wiązania jest znacznie zmniejszona.
Dlatego wstępna obróbka części jest warunkiem wstępnym uzyskania dobrych wyników w całym procesie galwanizacji. Przede wszystkim należy zapewnić odpowiednie stężenie i czystość roztworu odtłuszczającego i trawiącego. Po drugie, gdy roztwór odrdzewiający osiągnie pewną ilość zanieczyszczeń, wpłynie to na jakość powłoki, dlatego należy go regularnie wymieniać.
(2) Czynniki chemiczne w galwanotechnice
W procesie produkcji galwanicznej z różnych powodów do roztworu galwanicznego dostają się różne szkodliwe zanieczyszczenia. Istnieje wiele rodzajów zanieczyszczeń, w tym w przybliżeniu zanieczyszczenia metalami, tlenkami metali, zanieczyszczeniami niemetalami, różnymi nierozpuszczalnymi zawiesinami i zanieczyszczeniami organicznymi. Rodzaje zanieczyszczeń zawartych w różnych roztworach galwanicznych nie są takie same, a tolerancja na te same zanieczyszczenia jest również różna. Gdy jedno lub kilka szkodliwych zanieczyszczeń nagromadzi się w pewnym stopniu, będzie to miało wpływ na wydajność roztworu galwanicznego i jakość powłoki. Dlatego nie należy czekać, aż nagromadzenie zanieczyszczeń spowoduje szkody, zanim usunie się energię elektryczną.
Roztwór galwaniczny. Ponadto, zawartość każdego składnika roztworu galwanicznego ma optymalny zakres procesowy, a roztwór w zbiorniku powinien być regularnie testowany i analizowany, aby zapewnić, że każdy składnik mieści się w zakresie procesowym. Jednocześnie, w zależności od wielkości zadań produkcyjnych, rzeczywistych doświadczeń i wyników testów, następuje akumulacja zanieczyszczeń. Przed pogorszeniem jakości warstwy galwanicznej należy oczyścić roztwór galwaniczny, aby zapewnić stabilność roztworu galwanicznego.
(3) Czynniki kontrolne warunków procesu
Kontrola warunków procesu ma bezpośredni wpływ na jakość warstwy galwanicznej. Tylko dzięki opanowaniu i kontrolowaniu różnych warunków procesu dla każdego gatunku galwanicznego można uzyskać wysokiej jakości powłokę galwaniczną. Warunki procesu, takie jak temperatura, gęstość prądu, wartość pH i czas galwanizacji, muszą być odpowiednio dobrane. Na przykład podczas twardego chromowania temperatura i gęstość prądu nie są odpowiednio dobrane, co ma duży wpływ na wydajność prądu katodowego, zdolność do dyspersji, twardość powłoki i jasność roztworu chromu. Jak pokazano na poniższym rysunku, gdy temperatura jest wysoka, należy odpowiednio zwiększyć gęstość prądu, aby uzyskać pożądaną powłokę. Te dwa czynniki wzajemnie się ograniczają - jeśli zmieni się jeden z nich, drugi musi się odpowiednio zmienić. Dlatego, jeśli warunki procesu nie są dobrze kontrolowane, może dojść do wypadków związanych z jakością galwanizacji.
2. Czynniki zewnętrzne
Jako część ogólnej jakości części wyrobu, na jakość galwaniczną części wpływa nie tylko proces galwaniczny i wewnętrzne ogniwa galwanizerni, ale także w różnym stopniu inne ogniwa produkcyjne oraz działy produkcyjne i techniczne przedsiębiorstwa. Czynniki te często bardzo łatwo jest zignorować. Powinniśmy mieć pełną wiedzę na temat tych czynników.
(1) Czynniki projektowe
Projektanci wyrobów często zwracają uwagę tylko na kształt, rozmiar, dokładność obróbki i inne czynniki części wyrobu w procesie projektowania rysunków części, a nie biorą pod uwagę technologii obróbki części, zwłaszcza procesu galwanizacji, co powoduje wiele niepotrzebnych kłopotów w pracy galwanizera. Jednocześnie ma to pewien wpływ na jakość wyrobu.
1. Wpływ kształtu części na jakość galwanizacji.
Zdolność rozpraszania elektrolitu chromowego jest bardzo niska. Koncentracja prądu w narożnikach i końcówkach części łatwo powoduje powstawanie lokalnych wad, takich jak zadziory, przypalenia i guzki. W przypadku części o bardziej złożonych kształtach, głębokie wgłębienia i powierzchnie wewnętrzne często nie są pokrywane galwanicznie, co nie pozwala na osiągnięcie pożądanego efektu. Chociaż dzięki zastosowaniu anod piktograficznych, katod ochronnych i anod pomocniczych można uzyskać powłoki o możliwie równomiernej grubości, to nieuchronnie spowoduje to duże kłopoty podczas prac galwanicznych, a koszt galwanizacji znacznie wzrośnie. Dlatego projektanci powinni wnikliwie analizować proces projektowania, a rzemieślnicy powinni wzmocnić kontrolę procesu. Anody piktogramowe, katody ochronne i anody pomocnicze należy stosować tylko wtedy, gdy jest to absolutnie konieczne.
2. Wpływ zespołu na jakość galwanizacji.
Tak zwany zespół odnosi się do części, której nie można zdemontować po zespawaniu lub zanitowaniu wielu części. Przykładem niektórych produktów jest połączenie płyty podpierającej taśmę aksamitną z górnym, górnym i dolnym urządzeniem czyszczącym ramy wiórowej serii wrzecion podwieszanych. Jest to kompletny zestaw do galwanizacji. Podczas procesu galwanizacji roztwór chemiczny wnika w szczeliny części. Z jednej strony, po umieszczeniu części na pewien czas po galwanizacji, elektrolit ukryty w szczelinach wycieka i wchodzi w reakcję z warstwą galwaniczną, powodując rdzewienie części. Z drugiej strony, ze względu na przenikanie cieczy chemicznej, ciecz chemiczna z poprzedniego procesu nie może być dokładnie oczyszczona, zanieczyszczając ciecz chemiczną z następnego procesu, powodując zanieczyszczenie cieczy chemicznej i wpływając na jakość galwanizacji. W związku z tym przy projektowaniu należy w jak największym stopniu unikać galwanizowania całego zestawu złączy i w jak największym stopniu rozważyć po galwanizacji poszczególnych części, a następnie nitowanie lub zastosowanie innych metod montażu.
3. Rysunek nie jest wyraźnie oznaczony.
Tradycyjnie, części, które mają być galwanizowane, są po prostu zaznaczone na rysunkach, ale główne powierzchnie galwanizowane nie są wyraźnie zaznaczone, co sprawia, że konkretne operacje łatwo mogą być mylone. W przypadku głównych części proces galwanizacji musi zapewniać wewnętrzną i zewnętrzną jakość powłoki, a ponadto nie powinna występować oczywista aberracja chromatyczna. Dlatego tylko wtedy, gdy części główne i drugorzędne są zaznaczone na rysunku, można odpowiednio dobrać wieszak, aby uniknąć porażenia prądem podczas procesu galwanizacji, oraz określić położenie montażowe części, tak aby zadbać o części główne i drugorzędne, a także o ochronę izolacyjną. Aby zapewnić jakość galwanizacji.
(2) Czynniki powierzchniowe przed galwanizacją
Jakość powierzchni części przed galwanizacją ma poważny wpływ na jakość galwanizacji. Powłoka utworzona na płaskiej i gładkiej powierzchni jest zawsze lepsza niż powłoka utworzona na powierzchni chropowatej. Obróbka skrawaniem, ciągnienie na zimno i inne procesy wytwarzania części przed galwanizacją, tylko po to, aby zapewnić, że rozmiar, tolerancja kształtu, wykończenie powierzchni itp. przetwarzane w tym procesie są kwalifikowane, a rdza, zgorzelina tlenkowa, trudne do usunięcia zabrudzenia, nierówności itp. na powierzchni części spowodują, że części po galwanizacji Wygląd nie spełnia standardowych wymagań projektowych i użytkowych. Ponadto, stan powierzchni niektórych części jest niespójny po wejściu do procesu galwanizacji. Na tej samej części znajdują się zarówno części precyzyjnie obrobione, jak i części z silną rdzą i zgorzeliną, co uniemożliwia obróbkę wstępną. Zbyt krótki czas trawienia spowoduje utlenianie. Nie można usunąć zgorzeliny tlenkowej na części ze skórą i nie można przeprowadzić galwanizacji. Jeśli czas trawienia jest zbyt długi, części o dokładnych wymiarach ulegną korozji i zostaną zezłomowane. Prawidłową metodą powinno być przeprowadzenie obróbki wstępnej, takiej jak piaskowanie lub trawienie, w celu usunięcia powierzchniowej zgorzeliny tlenkowej z materiału silnie skorodowanego i zawierającego zgorzelinę tlenkową, a następnie przeprowadzenie obróbki mechanicznej w celu uzyskania powierzchni o jak największej jednorodności dla ostatecznej obróbki galwanicznej części.
(3) Czynniki harmonogramu produkcji
Ponieważ procedury przetwarzania wielu części muszą być przekazywane do wielu warsztatów, a galwanizacja jest zawsze ostatnim procesem, często części jeszcze nie dotarły.
W warsztacie galwanicznym, warsztat montażowy czeka już na części do zmontowania. Taka sytuacja powoduje, że okres budowy jest zbyt krótki i często konieczne są ciągłe zmiany, aby nadążyć za okresem budowy. Łatwo jest spowodować, że czas galwanizacji nie spełni wymagań procesu, lub że światło robocze w nocy nie jest jasne, co wpływa na jakość galwanizacji. Dlatego dział produkcji powinien koordynować okresy obróbki w każdym warsztacie, aby osiągnąć zrównoważoną produkcję i zapewnić czas obróbki procesu galwanicznego w celu wytworzenia kwalifikowanych wyrobów galwanizowanych.
(4) Czynniki związane z przechowywaniem i pakowaniem
W warunkach atmosferycznych metale żelazne są pokrywane cynkiem, aby zapobiec korozji. Jednakże, gdy powłoka cynkowa wejdzie w kontakt z farbą fenolową, farbą alkidową, tworzywem fenolowym, wilgotnym drewnem, sklejką itp. Im dłuższy czas, tym grubszy jest produkt korozji. Jest to niewielka ilość lotnych związków organicznych. Przyspieszenie korozji nazywane jest korozją atmosferyczną. Substancje, które mogą wytwarzać taką organiczną atmosferę lotną, to: farba, plastik, żywica, drewno itp. Szybkość korozji atmosferycznej jest ściśle związana ze stężeniem lotnej atmosfery organicznej. Im wyższe stężenie, tym silniejsza korozja. Jednak organiczna atmosfera lotna może powodować korozję powłoki cynkowej tylko w wilgotnej atmosferze. Jeśli jest tylko atmosfera korozyjna, a otaczające powietrze jest bardzo suche, korozja w zasadzie nie wystąpi. Dlatego w atmosferze tylko wtedy, gdy nie ma organicznej atmosfery lotnej lub jest ona całkowicie sucha w warunkach powietrznych, powłoka cynkowa jest niezawodną powłoką ochronną. W procesie przechowywania części zakwalifikowanych do galwanizacji należy zapewnić odpowiednie środowisko w magazynie, aby uniknąć korozji atmosferycznej części. Ponadto, podczas transportu, opakowanie produktu ma bezpośredni wpływ na odporność części na korozję. Dlatego należy zminimalizować źródło lotnej atmosfery organicznej. Części ocynkowane muszą być przechowywane w drewnianych skrzyniach, z niezawodnym opakowaniem wewnętrznym i środkiem osuszającym, aby zapewnić, że części są całkowicie odizolowane od zewnętrznej atmosfery korozyjnej, w przeciwnym razie części są bardzo łatwe do rdzy, wpływając na jakość produktu i powodując niekorzystne skutki. Te czynniki zewnętrzne są bardzo łatwe do zignorowania przez nas i stają się ważnym czynnikiem wpływającym na jakość galwanizacji.
3. Wnioski
Jako szczególny rodzaj pracy w przemyśle produkcyjnym, galwanizacja jest niezbędna, ale często jest ignorowana. Gdy pojawia się problem z jakością, szuka się przyczyny w procesie galwanizacji, ignorując inne czynniki zewnętrzne. Dlatego, aby zapewnić jakość wyrobów galwanizowanych, nie tylko warsztat galwanizacyjny, ale cały system kontroli jakości musi mieć jasno określone obowiązki i uprawnienia, w miarę możliwości w zakresie procesu galwanizowania, aby zapewnić dobre podłoże dla procesu galwanizowania. Od projektu rysunku technicznego do przygotowania procesu i oprzyrządowania, od obróbki części, montażu, kontroli do przeładunku i magazynowania, do końcowego pakowania i transportu, każde ogniwo powinno być ściśle kontrolowane w celu zapewnienia jakości galwanizacji, co ma bardzo duże znaczenie praktyczne dla poprawy jakości wyrobów.