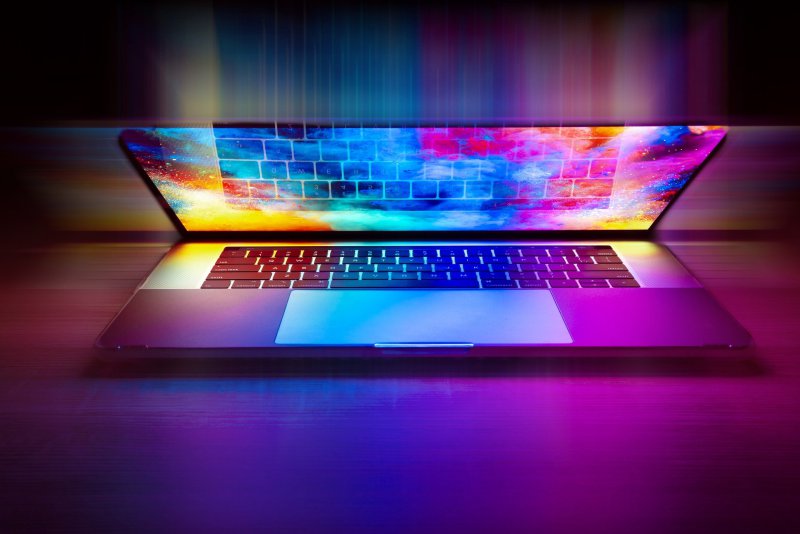
Aluminiowe części precyzyjne i produkty są popularne ze względu na ich niewielką wagę i wspaniały wygląd, a także coraz szersze zastosowanie w przemyśle i codziennych potrzebach. Wraz z ciągłym postępem nauki i technologii, zapotrzebowanie ludzi na różnorodność produktów staje się coraz silniejsze. Dlatego wymagania technologiczne stawiane produktom ze stopów aluminium są coraz wyższe, a zapotrzebowanie rynku coraz większe. W celu zaspokojenia potrzeb ludzi w zakresie różnorodności i wysokiej jakości produktów ze stopów aluminium, producenci obróbki CNC stopów aluminium podsumowują umiejętności procesowe podczas przetwarzania i problemy, na które należy zwrócić uwagę w obróbce CNC aluminium.
1. Wybierz odpowiednią metodę obróbki
Cięcie CNC jest metodą przetwarzania, która racjonalizuje cięcie i jest również powszechnym procesem w precyzyjnej obróbce aluminium. Wykorzystuje frezy z wielokierunkowymi funkcjami cięcia, interpolację cięcia spiralnego i interpolację cięcia konturowego. Niewielka liczba otworów jest obrabiana przez niewielką liczbę narzędzi.
2. Frez kulowy może być stosowany z interpolacją spiralną do ciągłej obróbki otworów stożkowych.
Kulowe frezy końcowe i wiertła z interpolacją spiralną mogą być używane do wytaczania i fazowania. Frez współpracujący z interpolacją konturową może wykonywać obróbkę półwykańczającą i obróbkę precyzyjną otworów. Frez końcowy do obróbki gwintów może być używany z interpolacją spiralną do obróbki różnych otworów gwintowanych.
W przypadku obróbki precyzyjnych części ze stopów aluminium o wysokiej wydajności, w celu uzyskania precyzyjnych otworów o dowolnej wielkości, można wykorzystać funkcję interpolacji narzędzia. Szczególnie w przypadku frezowania z dużą prędkością obciążenie każdego zęba jest stosunkowo niewielkie. Dlatego ten sam frez z węglika spiekanego może być stosowany do szybkiej i precyzyjnej obróbki otworów w różnych materiałach.
Ponadto, konieczne jest opanowanie techniki obróbki i umiejętności obróbki w zakresie obróbki aluminium CNC.
3. Wybierz rozsądną ilość cięcia
Personel może wybrać prędkość cięcia w zależności od przetwarzanego materiału, jego twardości, stanu cięcia, rodzaju materiału i głębokości cięcia. Warunki te są niezbędne do skutecznego zmniejszenia zużycia maszyny.
4. Wybierz odpowiednie narzędzie.
Kąt natarcia: Pod warunkiem zachowania wytrzymałości krawędzi skrawającej należy odpowiednio dobrać kąt natarcia, aby był większy. Jedna strona może szlifować ostrą krawędź, co może również zmniejszyć odkształcenia skrawania, sprawić, że usuwanie wiórów będzie bardziej płynne oraz zmniejszyć siłę i ciepło skrawania. Nigdy nie należy używać narzędzi o ujemnym kącie natarcia.
Kąt natarcia: Wielkość kąta natarcia ma bezpośredni wpływ na zużycie powierzchni bocznej i jakość powierzchni obrobionej. Grubość skrawania jest ważnym warunkiem doboru kąta odciążenia. Podczas frezowania zgrubnego, ze względu na duży posuw, duże obciążenie skrawania i duże wydzielanie ciepła, wymagane są dobre warunki odprowadzania ciepła z narzędzia. Dlatego kąt natarcia powinien być mniejszy. Podczas frezowania wykańczającego krawędź skrawająca musi być ostra, aby zmniejszyć tarcie między powierzchnią czołową a obrabianą oraz aby zmniejszyć odkształcenia sprężyste. Dlatego należy wybrać większy kąt wypukłości.
Kąt rozwarcia: Aby frezowanie przebiegało gładko, a siła frezowania była mniejsza, należy wybrać jak największy kąt spirali.
Kąt wejścia: Odpowiednie zmniejszenie kąta wejścia może skutecznie poprawić warunki odprowadzania ciepła i obniżyć średnią temperaturę w obszarze obróbki.
Zmniejszenie liczby zębów frezu i zwiększenie przestrzeni na wióry.
Ze względu na większą plastyczność stopu aluminium, większe odkształcenia skrawania podczas obróbki i większą przestrzeń na wióry, dolny promień kieszeni na wióry powinien być większy, a liczba zębów frezu mniejsza. Na przykład frezy poniżej φ20 mm mają dwa zęby, a frezy o φ30-φ60 mm lepiej jest stosować trzy zęby, aby uniknąć deformacji cienkościennych części ze stopu aluminium spowodowanych zatykaniem się wiórów.
Zęby do dokładnego szlifowania: Wartość chropowatości krawędzi tnącej zębów powinna być mniejsza niż Ra=0,4um. Przed użyciem nowego noża należy lekko naostrzyć przednią i tylną część zębów za pomocą drobnoziarnistego kamienia olejowego, aby wyeliminować resztki zadziorów i niewielkie ząbkowania powstałe podczas ostrzenia zębów. W ten sposób można nie tylko zmniejszyć ciepło cięcia, ale także stosunkowo zmniejszyć deformację cięcia.
Ścisła kontrola standardu zużycia narzędzia: Po zużyciu narzędzia wzrasta wartość chropowatości powierzchni obrabianego przedmiotu, wzrasta temperatura cięcia i zwiększa się odkształcenie obrabianego przedmiotu. Dlatego, oprócz wyboru materiałów narzędziowych o dobrej odporności na zużycie, standard zużycia nie powinien być większy niż 0,2 mm, w przeciwnym razie łatwo jest wytworzyć narastającą krawędź. Podczas cięcia temperatura przedmiotu obrabianego nie powinna zasadniczo przekraczać 100°C, aby zapobiec jego deformacji.
5. Wybierz rozsądne zamocowanie.
Części muszą w pełni odpowiadać potrzebom maszyny, aby ograniczyć niepotrzebne błędy pozycjonowania, należy też wybrać specjalne narzędzia mocujące.
6. Wyznacz rozsądną trasę obróbki.
Należy starać się jak najbardziej skrócić drogę obróbki, aby zmniejszyć zużycie maszyny.
W przypadku obróbki szybkościowej, ze względu na duży naddatek na obróbkę i obróbkę przerywaną, proces frezowania często powoduje drgania, co wpływa na dokładność obróbki i chropowatość powierzchni. Dlatego proces szybkiego cięcia CNC można ogólnie podzielić na: obróbkę zgrubną-półwykończeniową, obróbkę czystego naroża, obróbkę wykańczającą i inne procesy.
W przypadku części o wysokich wymaganiach dotyczących precyzji czasami konieczne jest wykonanie wtórnego półwykończenia, a następnie wykończenia. Po obróbce zgrubnej części można schłodzić w sposób naturalny, aby wyeliminować naprężenia wewnętrzne spowodowane obróbką zgrubną i zmniejszyć odkształcenia. Margines pozostawiony po obróbce zgrubnej powinien być większy niż wielkość odkształcenia - zazwyczaj 1 -2 mm. Podczas obróbki wykańczającej, na powierzchni wykańczanej części należy zachować równomierny naddatek na obróbkę, zwykle 0,2-0,5 mm, tak aby narzędzie znajdowało się w stabilnym stanie podczas procesu obróbki, co może znacznie zmniejszyć odkształcenia skrawania, uzyskać dobrą jakość obróbki powierzchni i zapewnić dokładność produktu.